Kit Assembly in Acumatica is a simplified method to combine multiple stock (or non-stock) items into a single inventory item without requiring a full manufacturing process.
i.e. is a process that allows businesses to combine multiple inventory items into a single sellable item, known as a kit. It’s a alternative to full manufacturing and is ideal for product bundling, prepackaging, or light assembly operations.
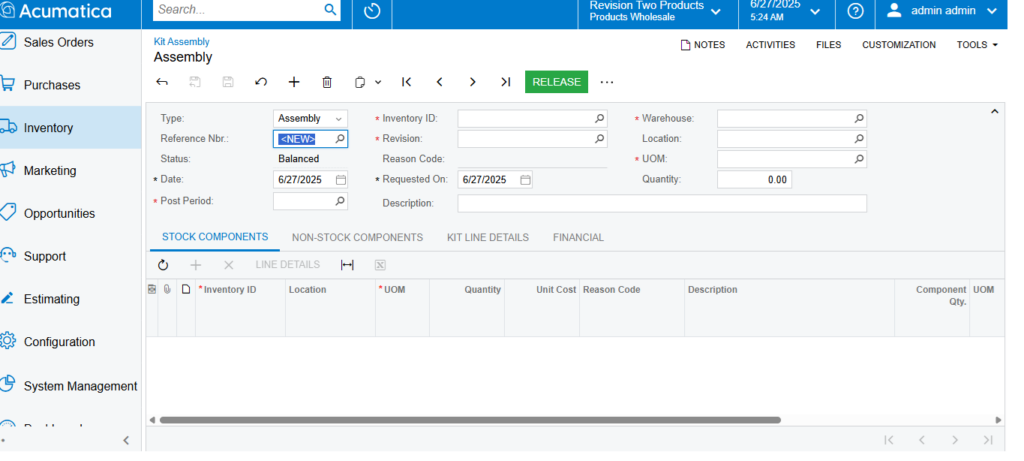
Purpose of Kit Assembly:
- Bundle Products for Sale:
- As one Product you want to sell a combo pack or gift set (e.g., Brush for paint + Different Color + Box)
- The system reduces individual items from inventory and add new stock quantity for the kit item after assemble.
- Simplify Sales Process :
- Easier for sales reps to sell pre-defined combinations of items.
- Instead of entering multiple lines on the sales order, you just enter the kit item.
- Track Inventory stock Movement:
- How many Components have been consumed.
- How many Kits have been created.
- Easy to Maintain Inventory Management.
- Helps to Warehouse Team Operation:
- Warehouse team can schedule and track kit production
- Warehouse team know which components are need to build kits.
- Pre-Assembled Inventory:
- Assemble Kits in Advance
- Disassembly Support:
- When you assemble the kit and somehow broken, the disassembly process is available, just reverse it.
Use & Benefits:
- Kit Assembly is ideal for businesses that bundle, package, or lightly assemble products before selling them.
- Combine individual items (e.g., Electronic tools, Foods, Medical Devises) into a ready-to sell packed product, perfect for seasonal promotions or combo offers.
- No Production Stages, Labor Tracking, MRP Setup Require, this is Ideal for simple assemblies.
- Most Important thing is, it Reduces Inventory Errors, automatically adjusts stock quantities when kits are assembled and disassembled, keeping inventory accurate.
- This Process support any industries like retail, pharma, distribution, or light manufacturing.
For example, if you sell a “First Aid Kit” containing a Band Aid, Adhesive Tape, Absorbent Cotton Bundle, Gauze Bandage, Gauze Pads, Oval Eye Pad, Anti-Septic Solution, Scissor…. etc. Kit Assembly lets you pre-assemble these components into one sellable SKU.
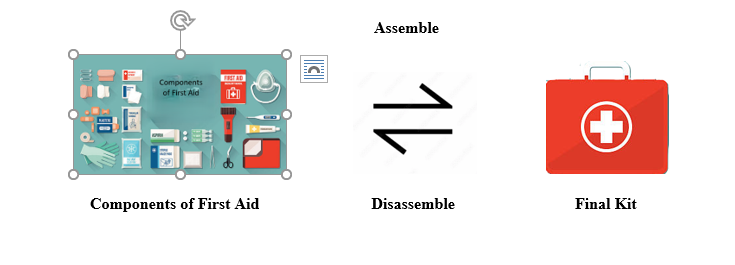
Kit Assembly vs. Manufacturing in Acumatica
Feature | Kit Assembly | Manufacturing |
For Simple Packing | √ | X |
Tracks labor, Material, Stages, Time, Cost, | X | √ |
Uses Production Orders | X | √ |
Fast Setup | √ | X |
Suitable For | Retail, distribution | Complex production |
When to Use and not to Use Kit Assembly:
- Use Kit Assemble if :-
- Labor, Material, Time, Tracking is not required
- Fastest Way to adjust the Inventory
- Packed Bundle items in to sealable unit.
- Don’t Use Kit Assembly if :-
- Require Detail Manufacturing
- Require Detail Costing (Labor, Overhead, Material)
- Relay On MRP
- Need Help with Acumatica Kit Assembly :-
Visit At: https://www.greytrix.com